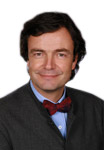
Hans-Georg Baunach
Welcome to the first issue of the Baunach Newsletter
Dear Ladies and Gentlemen,
Welcome to the first issue of the new rendePOST. In this way, we would like to inform you not only about innovations from our company, but also share useful experience and knowledge with you. We therefore hope that you will take a keen interest in this issue and provide us with suggestions and feedback on the specialist topics covered.
Hydraulics is an exciting and important topic when it comes to building highly efficient heating systems. And this will become even more important in the future in view of rising prices and an increasingly difficult outlook for the future. It's good for those who think about tomorrow today: investing in their own heating system pays off much better than investing money at today's interest rates! So you too should be able to say in future: Better informed thanks to rendePOST
Yours sincerely, Hans-Georg Baunach
Professional tip: Buffer connection on one side
A simple way to improve stratification in the buffer
It is very common to see in hydraulic plans and installations that heat generators and heat consumers are connected to buffer tanks in separate connections for each height (top, bottom, possibly also centrally). However, this often has a negative effect on the flow and thus on the stratification of the buffer tank, as the following example illustrates. Let's assume that a 28kW log boiler (90°C flow temperature) loads a buffer storage tank, while at the same time a radiator circuit (70/50°C) and a floor circuit (40/30°C) are supplied with a total of 14kW. Let us further assume that the two heating circuits are connected to the buffer by rendeMIX return utilisation with 70/30°C in total. When the buffer is connected on both sides, the entire boiler volume flow flows into the buffer at the top left and is removed again at the bottom left. In addition, the entire system volume flow is taken out at the top right and fed back in at the bottom right. The following formula therefore applies:
Buffer water flow rate = boiler volume flow rate + system volume flow rate
This very easily leads to a mixing of different temperatures in the buffer, which results in the system flow (70°C) being colder than the boiler flow (90°C) and the boiler return (50°C) being warmer than the system return (30°C). This in turn increases the volume flows, because
Boiler volume flow = 6/7 × boiler output : boiler delta-T = 6/7 × 28kW : (90-50)K = 0.6m³/h
System volume flow = 6/7 × system output : system delta-T = 6/7 × 14kW : (70-30)K = 0.3m³/h
Water flow rate of the buffer = 0.6m³/h + 0.3m³/h = 0.9m³/h
If, on the other hand, the buffer is connected to the connecting pipe between the heat generator and the heat consumer with only one connection per buffer height, only the difference of both volume flows through the buffer instead of the sum:
Buffer water flow rate = Boiler volume flow rate - System volume flow rate
The associated lower water flow rate of the buffer improves the stratification, so that the system flow (90°C) now has the same temperature as the boiler flow (90°C) and the boiler return (30°C) has the same temperature as the system return (30°C). This in turn naturally reduces the volume flows, because
Boiler volume flow = 6/7 × boiler output : boiler delta-T = 6/7 × 28kW : (90-30)K = 0.4m³/h
System volume flow = 6/7 × system output : system delta-T = 6/7 × 14kW : (90-30)K = 0.2m³/h
Water flow rate of the buffer = 0.4m³/h - 0.2m³/h = 0.2m³/h
Due to the one-sided connection of the buffer, the water flow rate of the buffer was increased by 78% reduced. We indicate this one-sided connection of the buffer in our hydraulic diagrams by black dots in the buffer.
It is not necessary to place the buffer between the heat generator and the heat consumer. It can just as well be mounted on a branch line that runs from the connection line between the heat generator and the heat consumer.
This often means greater design freedom in the installation with reduced pipe length. In order to ensure the hydraulic decoupling associated with the installation of a buffer storage tank, however, the cross-sections of these pipes must be sufficiently dimensioned. This applies in particular when using differential pressure-controlled circulating pumps.
The Kolping House in Essen wins 1,400 hours
Even more than with a boiler, the purchase of a CHP represents an investment that must pay off. The annual operating hours play a decisive role in amortisation.
The Kolping House operates a guest house with a catering and hotel business in Essen. The heating system was renovated in 2009 and put into operation in the autumn. It consists of a CHP unit, a gas condensing peak load boiler, two buffer storage tanks connected in parallel and a hot water storage tank with a stratified charging system as well as several heating circuits.
The CHP was planned with 7,000 h/a. However, its remote monitoring indicates an actual running performance of 8,400 h/a. This additional gain of 1,400 hours was achieved through three innovative processes in heat distribution. The CHP loads the buffers via two-zone loading. The heating circuits are supplied by a combination of two-zone discharge and return utilisation. As a result, the CHP unit ran for 23.6 hours a day, while the peak load boiler was only required for 1.4 % of hot water operation in summer.
The operator of the Kolpinghaus in Essen is pleased with the shift in heat generation from the peak load boiler to the CHP unit for 1,400 hours, as his CHP unit with 4.7 kW(e) saves him around €1,382 on his annual electricity bill at an electricity price of around €0.21/kWh.