Automatic hydraulic balancing
Advantages at a glance
- Hydraulic balancing done in no time at all
- Dynamically controlled instead of fixed
- Average savings of 20% on heating costs
- Permanent solution without blockages
- Lower power consumption of the circulation pumps
- Can be used as individual room control for panel heating
- Greater comfort and Higher efficiency
- Far more possible applications than just for heating circuits
Hydraulic balancing
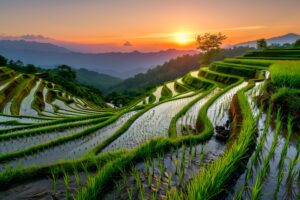
The purpose of hydronic balancing in a distribution network is to provide each consumer with the "right" amount of water. This must not be too small, because otherwise the consumer will not be adequately supplied; but it must not be too large either, because over-supply does not benefit the consumer, but only weakens the system and the other consumers then receive too little. However, because water always takes the path of least resistance, this does not happen by itself. The desired result will not materialise by itself, i.e. without active intervention in the various sub-strands of the distribution network. So the question is: what is the best way to achieve the goal of optimising the supply to all consumers?
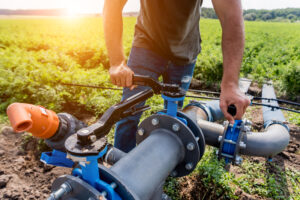
But with what effort and with what success?
One option is to carry out these interventions manually: You "simply" calculate the required water quantities, set the valves of the individual sections accordingly and that's it. That would be nice, because this method has several disadvantages: firstly, the calculation and subsequent adjustment of the individual water quantities is a lot of work and secondly, the result is difficult to check and also incapable of reacting to changing requirements: "flying blind in the fog", so to speak.
Better well regulated than fixed
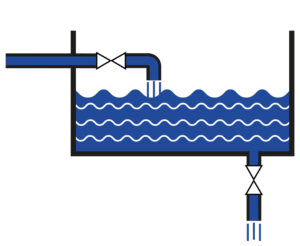
There is no feedback on the fill level to the inlet
Let's assume you wanted to "synchronise" the filling of a toilet cistern. Then you would ask yourself how many flushes are expected per day, for example, and set the supply accordingly. And everyone can imagine what happens if the users suffer from bowel disease or go on holiday.
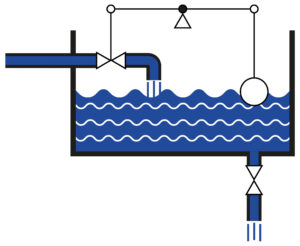
The fill level controls the inlet
This example is of course deliberately exaggerated and everyone knows how a toilet cistern is filled, namely via a float valve. And yet this example illustrates the difference between a fixed setting and a level control very aptly, because in contrast to a fixed setting, there is always information feedback in a control system, which adjusts the setting value accordingly: The higher the water level in the cistern, the lower the inflow or, when the desired level is reached, the inflow is switched off so that neither bowel diseases nor holiday trips can become a problem.
And what about "hydraulic balancing"? The "calculate and set" method is actually used here, although the calculation is often based on so many assumptions that the result has to be localised somewhere between coincidence and wishful thinking due to major inaccuracies - at least in existing buildings. If individual consumers are subsequently undersupplied, the system is "readjusted" (turned up) until it fits. And it only fits when no consumer complains. How optimal this end result is is anyone's guess.
So how could "automatic hydraulic balancing" work?
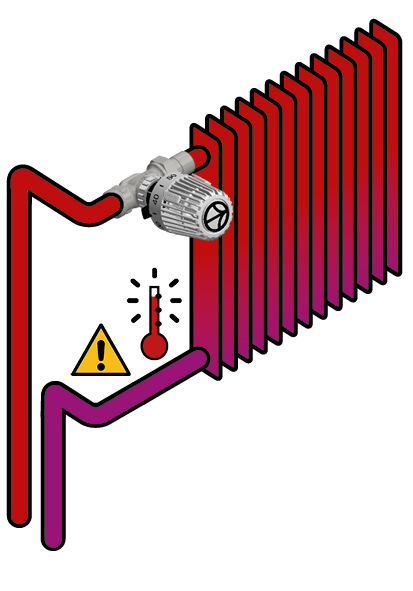
=> Return temperature too high
A heating surface of any type is a heat exchanger through which the heating water flows on one side and which is in contact with the medium to be heated on the other side. And what happens to such a heat exchanger if the primary (heat-conducting) heating water flow rate is too high? Quite simply: the amount of heat associated with the excessive flow rate cannot be completely dissipated, whereupon the return temperature, i.e. the outlet temperature of the heating water from the heat exchanger, rises. In other words, an excessively high return temperature is an indicator of an excessively high flow rate.
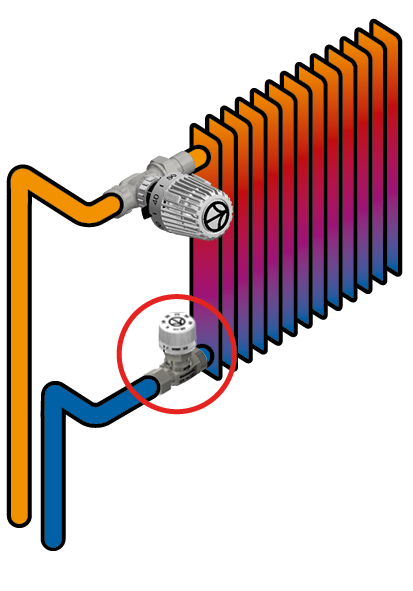
=> Return temperature low
And this is precisely where "automatic hydraulic balancing" comes in, utilising the principle of thermal control valves: if the return temperature is too high, the valve closes and the water volume is reduced; if the return temperature is too low, the valve opens and the water volume is increased. This is therefore a so-called return temperature limiter or RTB for short.
The target is the return temperature instead of the water volume
As the water volume is now the result of the control work of the RTB, it no longer needs to be calculated. Instead, the maximum return temperature to which the water volume is to be limited must be set. The prerequisite for this is, of course, a correctly designed heating surface, which we must always assume for any hydraulic balancing to be carried out. Nevertheless, we also know of examples that prove that the "thermal" procedure can also be used to compensate for the change in use of underfloor heating - e.g. from a bedroom to an office. (Technical article on hydraulic balancing)
Why minimum circulation?
In contrast to the above example of the toilet cistern, where the target variable "water level" is measured directly via the float and used to control the supply valve, the measurement of the return temperature is an indirect measured variable, as the change in the return temperature only occurs with a time delay after the change in the flow rate or the power consumed and also varies depending on the type and size of the heating surface. In other words, the delayed effect can cause the thermostatic valve to overreact.
If, for example, an air heater fan is switched off by the electric room thermostat, the return temperature from the heating coil rises very quickly and very sharply and the thermostatic valve closes completely. When the valve is closed, however, not only the flow is cut off but also the flow of information as to whether the air heater fan starts up again. A suitable small minimum circulation, on the other hand, maintains this information flow. In addition, the heating coil remains warm even when the fan is switched off, so that the minimum circulation not only improves the control quality, but also ensures frost protection and a warm start at all times.
Another example: if the ambient temperature of the RTB - e.g. in an underfloor heating circuit manifold cabinet - were above the setpoint value and such a valve were to close completely and switch off the flow completely, the valve body and thermostat would sooner or later reach the ambient temperature and the valve would therefore no longer open at all: a classic dead end. However, this operating state is reliably avoided by a suitable small minimum circulation.
Average savings of over 20%
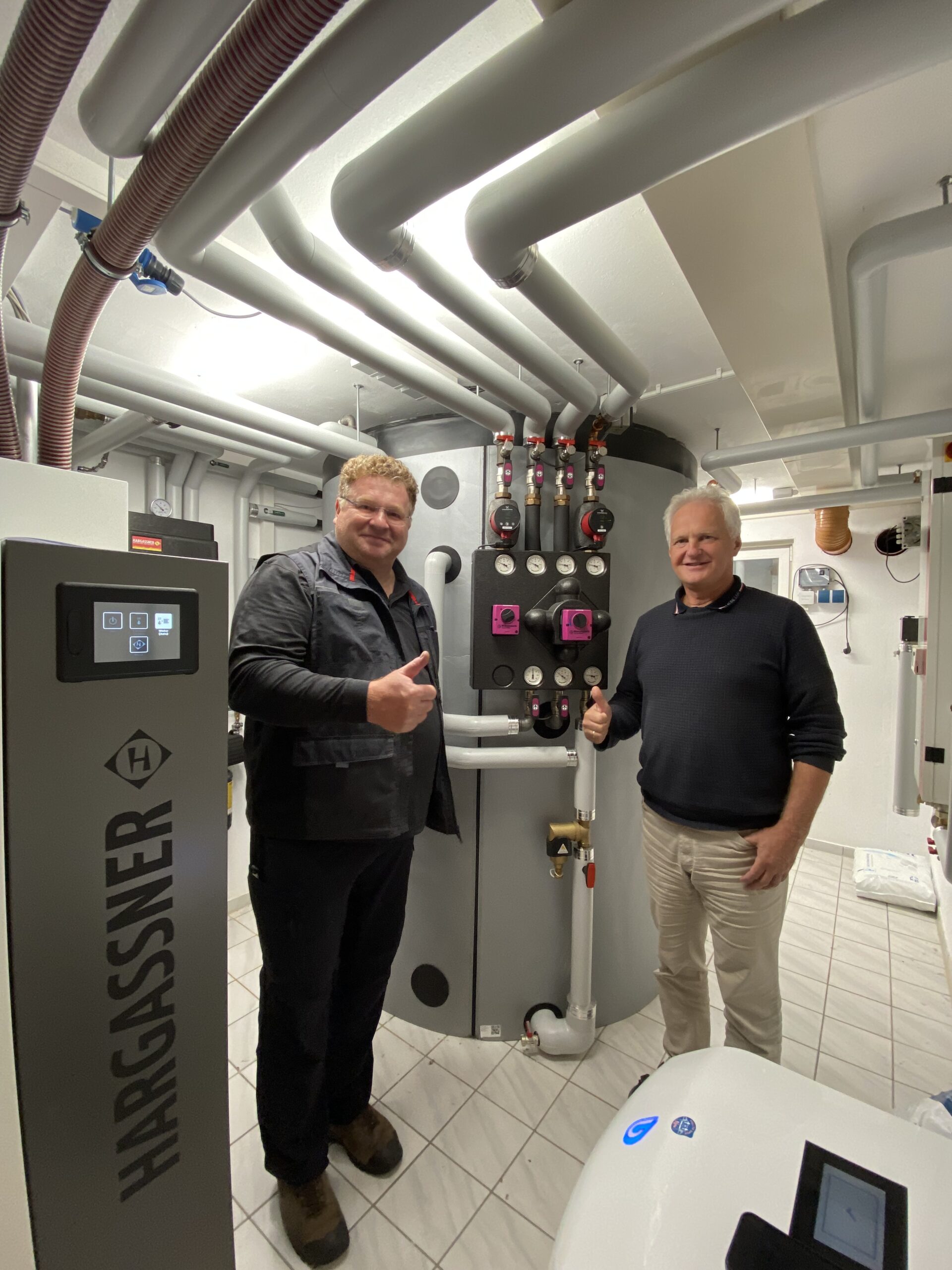
here with his customer Martin Gruber
Not all heating engineers realise that in the vast majority of heating systems, most of the waste cannot be avoided by replacing the heat generator, but only by completely renovating the hydraulic system.
But let's let an expert have his say:
"I claim that equipping two-family houses with Baunach stations and buffer storage tanks leads to energy savings of between 30 and more per cent. Of course, everything upstream and downstream of the Baunach station has to be right, right down to the integration of the pipes into the buffer cylinder, which is very often incorrect or inefficient. It is the most important link in a heating system. Boiler manufacturers promise you efficiencies of 92 and 93 per cent. This is of little use to me if the system is not optimised. I'm sure that many, even most heating systems achieve a maximum system efficiency of 75 per cent, and no more. Partly because high temperatures are mixed in the storage tank and the energy generator has to constantly react and switch. It is constantly reheating."
Lorenz Mayer, Heating-Sanitary-Solar, Petting
Permanent solution without blockages
Who hasn't experienced this: You've just calibrated the radiator heating circuit with presettable thermostatic valves according to all the rules of the art, and then the phone rings: "The radiator in the living room isn't getting really warm!" And what do you do then? You drive to the customer and "readjust". Since you can't and don't want to charge for this work, it has to "fit" the first time if possible. This is often caused by tiny impurities in the heating water that collect in front of the equally tiny openings of the pre-set valves, thus choking off the flow. Can this even happen with dynamically controlled thermostatic valves? Hardly, because these valves are not fixed, but control dynamically: too low a flow rate results in too low a return temperature and thus an opening valve that allows the impurity to pass through.
Lower power consumption of the circulation pumps
Of course, there are also dynamically regulating balancing valves, such as differential pressure or flow-controlled valves. What they have in common is that they have to draw their control work, i.e. the mechanical energy for opening and closing the valve, from the flow of the heating water. This means that these valves only function from a minimum pressure loss of usually around 200 mbar. Now you have to imagine this as follows: every cubic metre of water, which is known to weigh a tonne and which is balanced in this way, has to be pumped up an additional two metres, work which has to be purchased at high cost as electricity via the circulation pump. With the thermostatic valve, on the other hand, this energy comes from the heat of the heating water and the heat generator cannot even smile about this load, as it simply does not notice it at all.
Video description of the return temperature limiter (RTB):
The RTB valve is a thermostatic return temperature limiter with adjustable maximum temperature and fixed minimum flow in the order of 0.5% of the nominal flow.
The RTB eliminates the need to calculate and manually regulate volume flows, as the flow rate of each heating surface is automatically adapted to the actual output and the heating circuit is automatically hydraulically balanced. The setpoint for the maximum return temperature is simply set on the thermostatic head. If the return temperature exceeds this setpoint, the valve reduces the flow by closing without auxiliary energy. The heated heating water remains in the heating surface for longer and can therefore give off heat more effectively. Due to the fixed minimum flow rate, the valve reacts as quickly as possible to load changes.
Areas of application of the RTB
a) Radiator heating circuits (two-pipe systems):
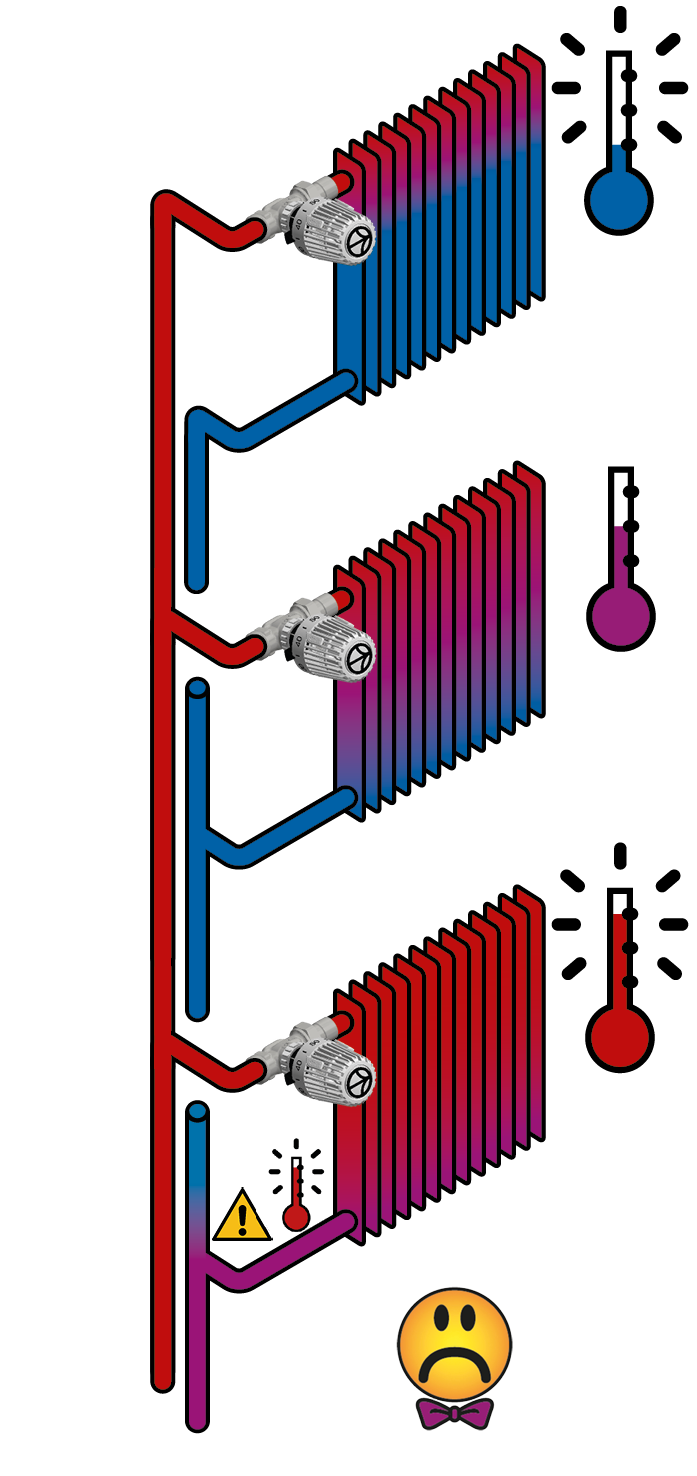
not evenly on the radiators
Radiator heating surfaces are automatically hydraulically equalised by the installation of RTBs. The mechanism is always the same: if the flow through the heating surface is too high, the return temperature is too high and vice versa. The RTB is set here to the lowest possible temperature, whereby the so-called "design" of the heating circuits must be taken into account. It is not necessary to calculate the water quantities for this process, which is a great advantage, especially in existing buildings.
The design of a heating circuit is defined as its maximum flow and return temperature on the coldest expected day for which the building's heating system is designed. In older buildings, for example, designs of 70/50°C or 60/40°C are common, while in newer buildings designs of 50/35°C or even 40/30°C are used. To ensure that the radiators can supply sufficient heat to the building despite the lower return temperature, the weather-compensated flow temperature should be increased accordingly after the RTB has been installed by correcting the so-called heating curve, e.g. the heating circuit is raised from 60/40°C without RTB to 70/30°C with RTB or from 50/35°C to 55/30°C.

The result of this thermostatic balancing is not only the complete equal distribution of heat to all radiators, which corresponds to the achievement of the planned comfort, but also a significant saving in heating costs due to lower return temperatures and lower electricity costs, because the amount of water to be pumped by the circulation pump is also significantly reduced. Even if it sounds unbelievable: in our experience, it is actually possible to operate radiator heating circuits with return temperatures of 35°C, 30°C and sometimes even 25°C if there are no major faults in the heating system and the flow temperature can be raised sufficiently. And all this - as already mentioned - without the time-consuming "calculation" of the water quantities, which is often only possible on the basis of assumptions, because these are set automatically and automatically in each individual load case. So if, for example, several radiators are switched off for a holiday, the remaining radiators still receive the same quantities of water, as their return temperature is not affected. The circulation pump running in the "constant pressure" operating mode adjusts its speed to the lower delivery volume without increasing the delivery pressure.
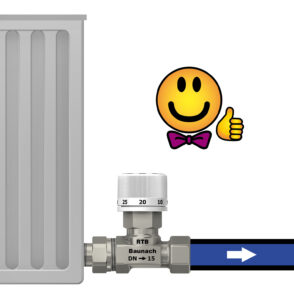
Radiator return fitting
The RTBs are fitted to each radiator instead of the lockable return screw connection, set to the desired maximum temperature and fixed to prevent adjustment. Due to the convection-related inflow of cold air at the radiator return, overshooting of the RTB at the radiator does not occur, nor does the dead end described above due to excessive ambient temperature. This is why our RTB valves in the so-called radiator version (wheel) do not have a minimum circulation (MUL), so that the connection to the pipework can still be shut off when the radiator is removed.
b) Underfloor heating circuits:
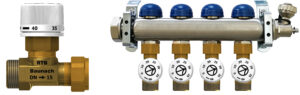
are mounted directly on the return collector of the distribution system
The RTBs in the underfloor heating version (Fbh) have a so-called Eurocone screw connection on both sides and can be fitted directly to the return manifold of the underfloor distribution system; a process that only takes a few minutes per valve with a little practice.
A good setting recommendation has proven to be to set the return temperature about two and a half degrees above the desired room temperature. Here too, it is advisable to adjust the weather-compensated (outdoor temperature-dependent) flow temperature slightly upwards and set the circulation pump to "constant pressure" operating mode.
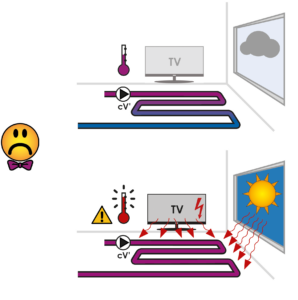
With underfloor heating systems - as with panel heating circuits in general - the heat is transferred to the room via radiation at lower temperatures. The return temperature is usually only a few degrees Celsius above the room temperature. As a result, the return temperature already increases when the room temperature rises, e.g. due to external heat input such as solar radiation or electrical appliances. Because a higher room temperature means that less heat is transferred from the heating surface to the room, this is known as the "self-regulating effect" of underfloor or panel heating.
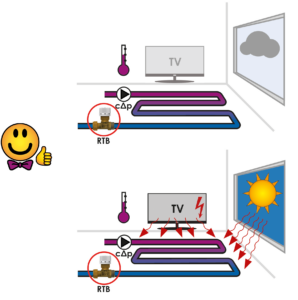
In the case of a floor or surface heating circuit that has been calibrated using a fixed setting, however, nothing happens because the fixed water flow rate is not affected. If, on the other hand, the balancing has been automated by installing an RTB, this also reduces the flow rate of the heating surface when the return temperature rises, which further reduces the heat output into the room. This not only increases the self-regulating effect, but also fulfils the requirement of the Energy Saving Ordinance (EnEV), namely that "heating systems with water as the heat transfer medium [...] must be equipped with automatic devices for room-by-room control of the room temperature when installed in buildings". In other words: By installing the RTB, room-by-room control of the room temperature is possible and thus fulfils the standard.
Compared to most individual room controls with room thermostats, RTBs have a further advantage because they work "proportionally", i.e. they can adjust the flow rate continuously, whereas most individual room thermostats are so-called two-point controllers (click-clack thermostats) that only switch the flow rate fully on or off. This has two disadvantages, one in terms of efficiency and the other in terms of comfort: efficiency is reduced because when the valve is fully open, too much water results in a high return temperature, whereas when the valve is closed, the heating surface makes no contribution to the return temperature. If it had a lower flow rate all the time, it would contribute to a low return temperature all the time. However, comfort is also reduced because two-point controllers necessarily have a hysteresis, i.e. an on/off switching differential: they only switch off when the room is too warm and only switch on when it is too cold. This results in cooled heating surfaces, which can lead to annoying complaints, especially with underfloor heating.
Only in rooms that are not to be constantly heated, such as children's or guest rooms, is the additional installation of such individual room controllers recommended, as they can be used to switch the room heating on and off very conveniently.
See for yourself how an RTB valve in less than three minutes is mounted on the return collector of a floor distribution system:
c) Radiator heating circuits (single-pipe systems):

All radiators open (full load)
In many existing residential buildings in the past, radiator heating circuits were built as so-called "single pipe systems". With this connection principle, the individual radiators are not connected in parallel to the flow and return of the supply pipes, but are connected in series, whereby a bypass must pass each individual radiator, because otherwise only all radiators could be operated together; if, on the other hand, one or more were switched off, all the others would also remain cold.

Not all radiators open (partial load)
One of the biggest problems with such systems is that the volume flow through all the bypasses must be kept as low as possible without restricting the total flow rate to such an extent that there is an undersupply at any of the radiators. In addition, there are practically no residential buildings that are supplied with a single single pipe run, but mostly those in which individual storey flats were designed as single pipe runs, which were then connected to the risers - usually in stairwells. This means that several single pipe runs are connected in parallel, whereby it is not uncommon for entire flats to be undersupplied compared to others. This problem is often "solved" by increasing the circulating water volume by installing larger pumps until sufficient heat reaches the last corner of the building, whereby the overall efficiency of the hydraulic distribution system is completely neglected.
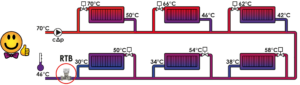
All radiators open (full load)
As the two illustrations opposite show, the amount of water in a single-pipe system depends on the heat output of all its heating surfaces. Such a quantity of water cannot be constant and therefore the calculation and fixed setting of such a quantity of water leads in the vast majority of load cases to a considerable surplus and thus to an enormous waste of thermal energy.

Not all radiators open (partial load)
Here too, RTB valves offer a solution that is as simple as it is perfect, because - as already described several times - they automatically and automatically adjust the amount of water based on the return temperature to the amount of heat actually emitted by the heating surfaces. At the same time, they reduce the amount of water circulating in all single-pipe systems to the minimum actually required, thereby increasing comfort by distributing the heat evenly. And finally, oversized circulation pumps and the electricity required to drive them are no longer needed. These RTB valves are always installed at the end of the return of each individual single-pipe line before it enters the supply line, which - as already mentioned - is often a riser in the stairwells.
For the first time in three decades?
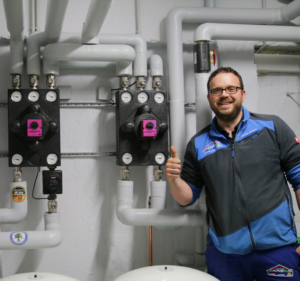
"I equipped a hotel with RTB DN15.
That didn't work for years either - now it's finally working!"
Many of our customers confirm time and again that they have been able to successfully balance single-pipe heating systems for the first time after many years of operation using the RTB. We also hear again and again that the retrofitting of buildings with single-pipe heating circuits with buffer storage tanks is practically only feasible by installing RTBs, as the buffer storage tanks can only fulfil their purpose if sufficient stratification - i.e. a sufficiently large temperature difference between "bottom" and "top" - is formed, which requires a low return temperature and water circulation limited to what is necessary.
But let's let an expert have his say:
"In the hotel mentioned, the RTBs were THE solution in the single-pipe system after more than 3 decades of 'non-functioning' radiators or 'randomised function'.
If you have any further questions, please do not hesitate to contact us.
With sunny greetings
Daniel Jansen
Master plumber & heating engineer - Expert for heat pump systems VDI 4645 - Building energy consultant - HWK certified bio-heat installer"
d) Domestic hot water storage tank:
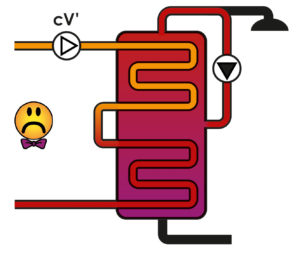
(partial load)
Many people do not realise that domestic hot water storage tanks also have heating surfaces or heat exchangers that should be balanced if you want to avoid excessively high return temperatures and the associated disadvantages for efficiency and comfort.
This is because an unregulated flow rate of heating water does not lead to faster hot water preparation, but on the contrary to a poorer efficiency of the heating system and often also to a longer duration of hot water preparation due to switching the heat generator on and off (cycling) and thus to a lower level of comfort.
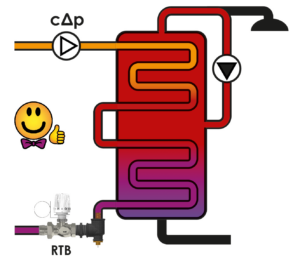
(partial load)
Strictly speaking, a distinction must be made between two very different operating modes for storage water heaters: Hot water preparation and hot water readiness.
No freshly tapped cold water is heated during hot water standby, only the cooling losses of the cylinder and the DHW circulation pipes are compensated. This is a weak load requirement at high temperatures. For this reason alone, a system that is not automatically balanced would result in higher return temperatures when hot water is being prepared. However, thanks to the RTB, this does not happen, or at least not unchecked, as the heating water flow rate is reduced to the lower standby requirement, and does so automatically.
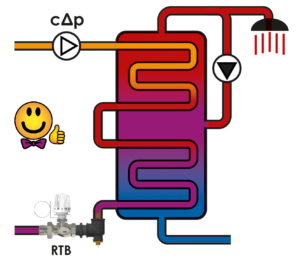
(full load)
During hot water tapping operation, on the other hand, cold water flows into the cylinder and extracts much larger quantities of heat from the heating water via the heat exchanger than in standby mode. The RTB in the return flow of the cylinder recognises this from the lower outlet temperature and opens so that more hot heating water flows through the heat exchanger. In this way, the amount of heating water is automatically adjusted to the actual heat requirement without the return temperature rising. This makes it possible to combine high efficiency with high comfort, which would be impossible to achieve with a fixed setting.
e) Air heater or air heating coil:
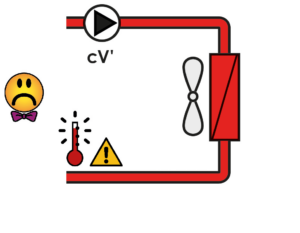
(partial load)
Air heaters are usually room thermostatically controlled fan-purged heat exchangers: once the room setpoint temperature is reached, the fan switches off while the heating water continues to flow unhindered through the heat exchanger. Even with a heating coil calibrated to nominal output, this must lead to an extraordinarily high increase in the return temperature; the same applies if the fan blower is not operated at full speed: the heat that is not completely removed leads to an increase in the return temperature.
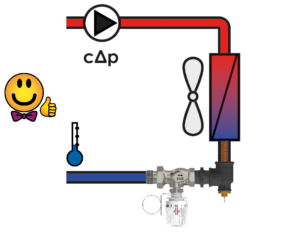
(partial load)
An RTB in the return of the heating coil, on the other hand, reacts to the rise in return temperature by immediately reducing the heating water flow rate. Again, the heating water flow rate is adapted to the actual heat requirement, the return temperature remains stable and the system operates with high efficiency.
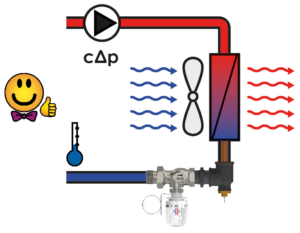
(full load)
As soon as the fan blower starts up, the return temperature drops rapidly and the RTB reopens the heating water flow rate. It does not matter whether the fan blower is running at a low or high speed, as the control of the heating water volume via the return temperature always guarantees the correct water volume. The small minimum circulation of the RTB guarantees a quick response and a warm start of the air heater at all times - comfort and efficiency are not a contradiction in terms.
Another tip from us: to minimise the reaction time when the air heater fan starts up, the RTB must be installed as close as possible to the output of the heating coil.
f) Radiant ceiling panels:
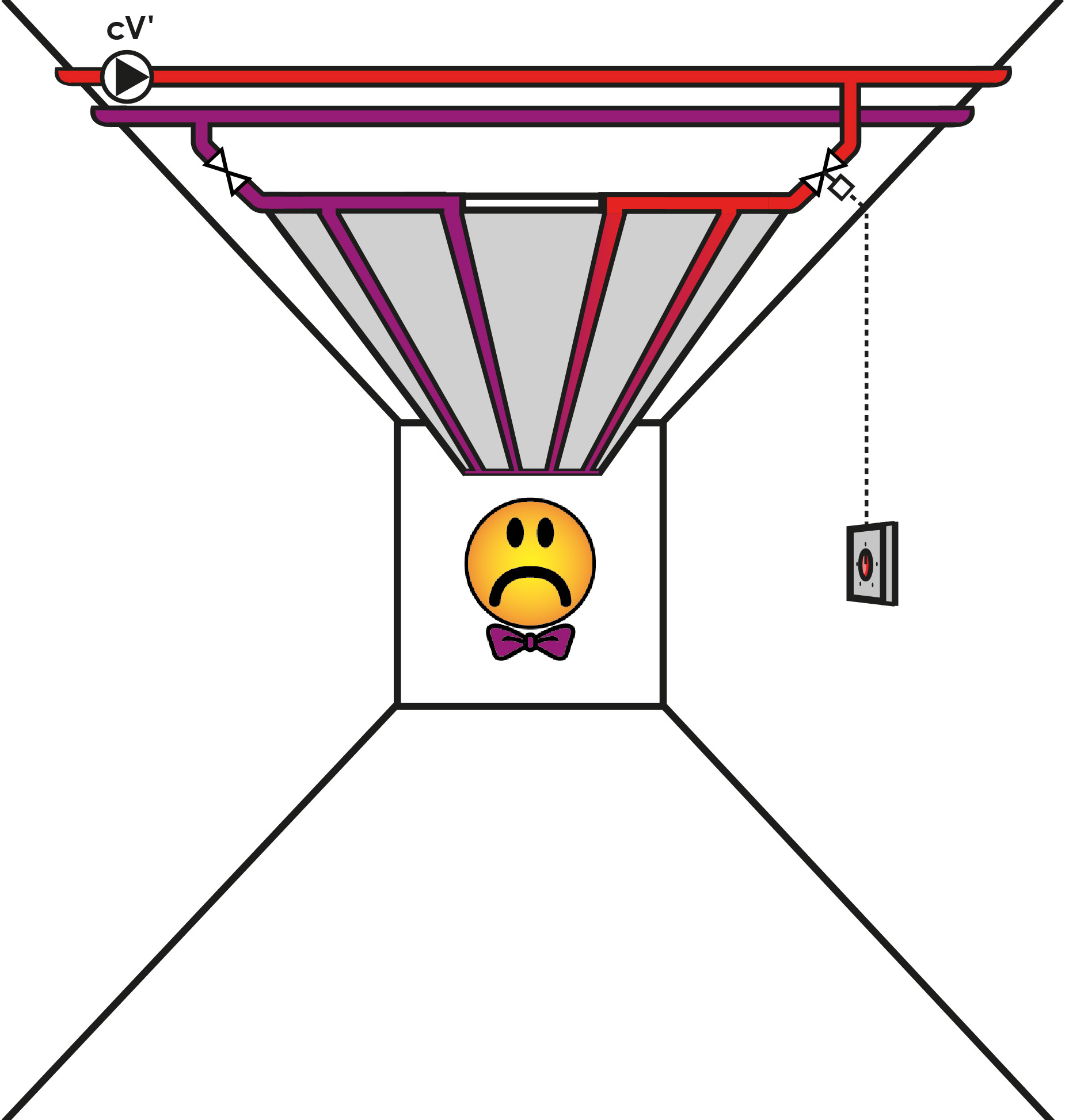
Radiant ceiling panels are radiant heating surfaces that are generally operated at higher temperatures than underfloor or wall heating surfaces. It is not uncommon for the heating water flow to be switched on and off via electric room thermostats.
When several radiant ceiling panels are connected in parallel, you have the same problem again of supplying all the heating surfaces with the "correct" quantities of heating water, this time usually also at lofty heights, where readjustment is particularly enjoyable.
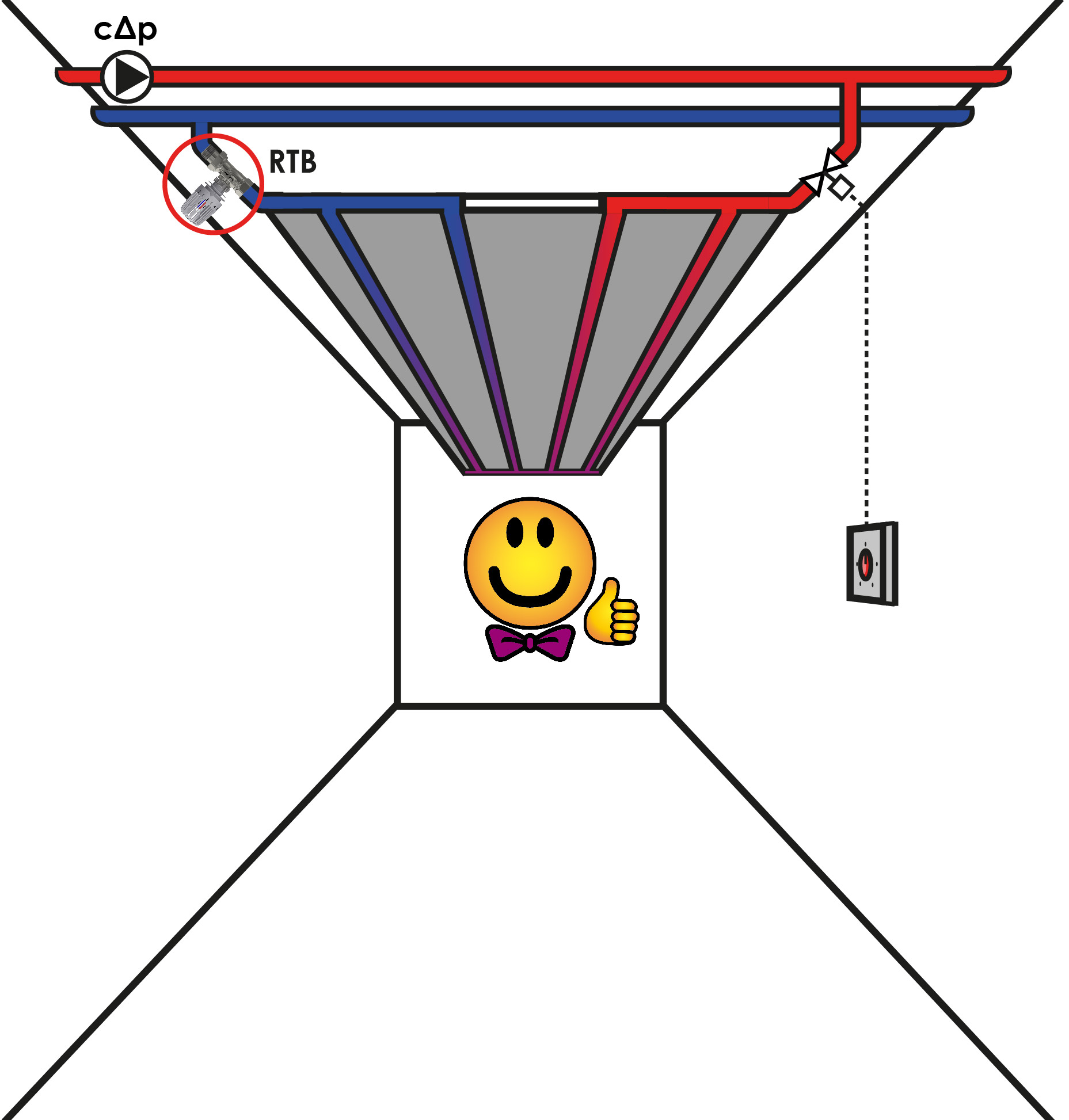
The use of RTBs eliminates this problem once and for all, because you simply set the desired return temperature for the design case and you're done! The return temperature can usually be reduced slightly, e.g. from 50 °C to 45 °C or perhaps even 40 °C, which further increases the desired savings effect.
Another little tip from us:
If you want to increase the performance of your radiant ceiling panels at lower temperatures, it is best to paint their radiating sides (undersides) in matt black.
g) Swimming pool water heat exchanger:

Even if their frequency of use is the exception rather than the rule, the same applies to swimming pool water heat exchangers as to all other heating surfaces: with an unchecked heating water flow rate, you generally only increase one thing, namely the waste potential of the heating system.
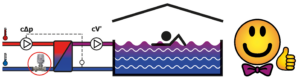
The solution would be so simple: install an RTB as close as possible to the outlet in the return flow and the problems are eliminated.
Our tip: It is best to set the circulation pump to the "constant differential pressure" (c∆p) operating mode right away, then it will automatically adjust its work input to the water volume, just as the RTB adjusts the water volume to the actual heating load.
f) Ventilation system or air conditioning system:
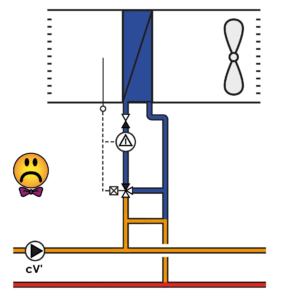
(partial load)
Ventilation and air conditioning (HVAC) systems differ from air heaters in that they generally have their own mixer circuit with autonomous control.
As this is often a trade boundary between heating and ventilation construction, the so-called bypass circuit is widely used to ensure that hot supply water is available at the air conditioning system at all times and that there is no risk of frost even when the outside air supply is below zero degrees. This functional principle corresponds to that of domestic hot water circulation.
However, anyone who has ever carried owls to Athens can ask themselves what an open bypass, i.e. water circulation without heat extraction, means for the efficiency of a heating system: it is gross nonsense!
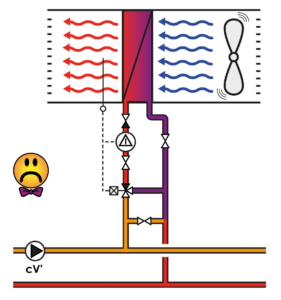
(full load)
This is because the open bypass often carries such large quantities of water that there is a significant increase in the return temperature even in normal operation and not just during standby mode.
Practical example:
On 16 February 2017, Hans-Georg Baunach spent the afternoon in the heating system of the Neuss ski hall, a building with a 1 MW natural gas boiler system. During his stay, he found exactly this situation and corrected the hydraulic setting by closing all bypass valves upstream of the air handling units and setting the pump on the manifold from constant speed to a constant differential pressure of 100 mbar.
Result:
The following year, €20,000 worth of gas was saved without anyone freezing.
Link to the technical article:
Skihalle Neuss - Many thousands of euros saved
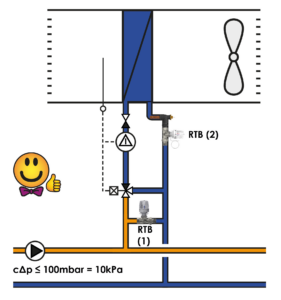
(partial load)
The solution is obvious: To maintain the frost protection and warm start function, replace the open bypass with an inert RTB (1) and set it to the lowest possible minimum temperature required to ensure frost protection and warm start, e.g. 30 °C. Do not be too generous here, because as soon as the system starts up, the water volume increases so quickly that the full flow temperature is usually still available during the system start-up.
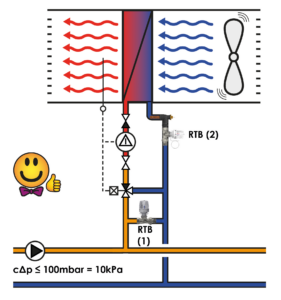
(full load)
For balancing the return flow from the heating coil in control mode, you can also use the quick RTB (2), which we have already used to automatically balance the air heating coils of the air heaters (see above). This can also be used to lower the return temperature of the air conditioning system's heating coil. In any case, you should try to set the circulation pump of the inner mixing circuit of the air conditioning system (I) to the lowest possible speed.
g) Buffer loading by condensing boiler without minimum circulation:
Likewise, only a few experts realise that not only the heating surfaces of all heat consumers should be balanced, but possibly also those of heat generators. The following example illustrates this:
You want to use a condensing boiler to keep the top zone of a buffer cylinder at a minimum temperature of 75 °C, for example, in order to be able to guarantee a sufficient pouring capacity in domestic hot water preparation. At the same time, however, the buffer should enable regenerative generators, such as a solar thermal system, a biomass boiler or a combined heat and power unit, to run for a sufficient period of time. It is clear that the condensing boiler will only achieve its highest efficiency with the coldest water from the lowest zone of the buffer.
If the sensor at the top of the buffer signals to the boiler that the temperature has fallen below the minimum temperature, the boiler and circulation pump will start up. However, if the flow rate is too high, the boiler will not even reach the required flow temperature because its delta-T is too small, which means that it will not switch off again.
The boiler only reaches the switch-off condition after it has fully charged the buffer and thus raised its own return temperature to such an extent that it reaches the switch-off condition - in our example of 75 °C - with its small delta T, which is a consequence of the volume flow being far too high.
In other words, when the peak load boiler has finished its work, the buffer is fully charged and the renewable generators are left behind - a nonsense that unfortunately happens all too often.
However, manual adjustment of the boiler throughput is hardly an option for two reasons:
1) The boiler output is usually variable.
2) The return temperature of the boiler is usually not constant.
For this reason, only a thermostatically controlled balancing of the boiler water flow can be considered, in which the boiler water volume is controlled in such a way that the desired minimum temperature of the buffer is guaranteed to be exceeded by the flow temperature of the boiler, e.g. by 5 K. As long as the boiler has not reached this 80 °C, the flow temperature limiter (VTB) remains in the closed state at its fixed minimum circulation. Only when the set minimum flow temperature is reached does the valve open and ensure that the buffer receives a top zone of at least 75 °C hot water, precisely defined via the sensor position.
As soon as the buffer sensor signals to the boiler that the target temperature has been reached, the boiler starts to reduce its output, which, thanks to the VTB, automatically leads to a reduction in the boiler water flow until the boiler finally switches off.
The question now arises as to how to get as much of the residual heat from the boiler as possible into the buffer, which is usually done via the pump run-on. And here, too, the VTB has a regulating effect, because it would of course be completely counterproductive if the temperature of the top zone of the buffer were to fall below the switch-on condition of the boiler again during this residual heat utilisation and the whole game continued until the buffer was fully charged by the peak load boiler in the end.
Return temperature manifold (RTM)...
The installation of a return temperature distributor feed-in set is generally recommended for fresh water or solar modules. Furthermore, other areas of application in which temperature fluctuations are to be expected. By using it, the feed can be carried out at the buffer at the correct temperature. This supports clean stratification and a high degree of utilisation of the heat bound in the buffer.
...Fresh water stations and solar systems (feed-in set)
The distribution temperature setpoint is adjusted at the thermostat head: Water above the setpoint flows through output red (hot), below the setpoint through output blue (cold). The valve can react quickly to temperature fluctuations thanks to the reaction time of the thermostatic head (5 seconds). We generally recommend the installation of such RTV feed-in sets for fresh water or solar modules and other applications where fluctuating feed-in temperatures are to be expected. The spiral immersion sensor and angled T-piece for optimum sensor mounting as well as matching screw fitting inserts complete this valve to make an easy-to-install feed-in set.
Flow temperature controller (FTC)...
The FTC products consist of a thermostatic flow-temperature controller in the form of a three-way mixing valve and a thermostatic head with sensing element. We have two different sets to choose from for different applications:
...Fresh water stations and solid fuel boilers and CHP (extraction set)
If heat is withdrawn from the buffer, e.g. by a fresh water station, the risk of calcification is reduced by limiting the temperature and at the same time the supply of hot water in the top zone of the buffer is extended - more drinking water can therefore be heated with the same heat content in the buffer because the buffer remains hot longer at the top but becomes cold more quickly at the bottom. If, on the other hand, heat is supplied to the buffer, it is initially only concentrated in the upper zone of the buffer until its temperature has reached the setpoint value and only then is it also conducted to the lower zone. The buffer therefore gets hotter faster at the top and stays cold longer at the bottom! An angled T-piece for optimal sensor mounting and matching screwed inserts complete this valve to an easy-to-install extraction set.
...Heating value peak load boiler at the buffer tank (heating value set)
By mixing boiler flow into the boiler return, the boiler flow temperature is constantly controlled to the set target value. For this purpose, the boiler circuit pump should be set to the highest possible output (stage III). In this way, the volume flow is adapted to the boiler output during buffer loading (stove!) and the flow temperature is kept constant even with variable boiler output. The buffer is always filled with equally hot water at the top, which is what makes precise top loading possible in the first place. In addition, the boiler is protected against condensation and subsequent cooling down of the hot zone during pump run-down (residual heat utilisation) is effectively prevented. Immersion sleeve and angled T-piece for optimum sensor installation as well as matching screwed inserts complete this valve to an installation-friendly heating value set.
Flow temperature limiter (FTL)...
The purpose of the FTL valve is to prevent a defined temperature from being exceeded. If there is a defect in the heater or mixer that causes the flow temperature to rise above the set value, then the pump is de-energised. This automatically regulates the heating process. This ensures special protection for the screed, the pump and above all the heat generator.
...for downstream flue gas heat exchangers of boilers and CHP units (Condenser Set)
If the flow temperature falls below the adjusted setpoint, the valve reduces the flow by closing without auxiliary energy. The heating water to be heated remains longer in the heat exchanger and can thus absorb more heat. Due to the fixed minimum flow rate, the valve always reacts as quickly as possible to load changes. The flow rate is adapted to the actual power absorbed and the heating circuit is automatically hydraulically balanced. Double nipples and an angled T-piece for optimum sensor installation make it a practical installation set.
...for condensing boilers without minimum flow and ∆T-limitation (condensing set)
The sensor monitors the flow temperature and throttles the water quantity if the temperature is below the setpoint. This enables a constant flow temperature with variable boiler output or fluctuating return temperature through variable water quantity with full condensing value utilisation. In buffer cylinders, the use of the VTB condensing set is manifested by the rapid build-up of a stable hot water zone in the uppermost buffer zone (stable top charge), a high level of hot water comfort, high regenerative utilisation rates and long boiler running times. Immersion sleeve and angled T-piece for optimum sensor installation as well as matching double nipples and heat-conducting paste complete this valve to an installation-friendly condensing set.